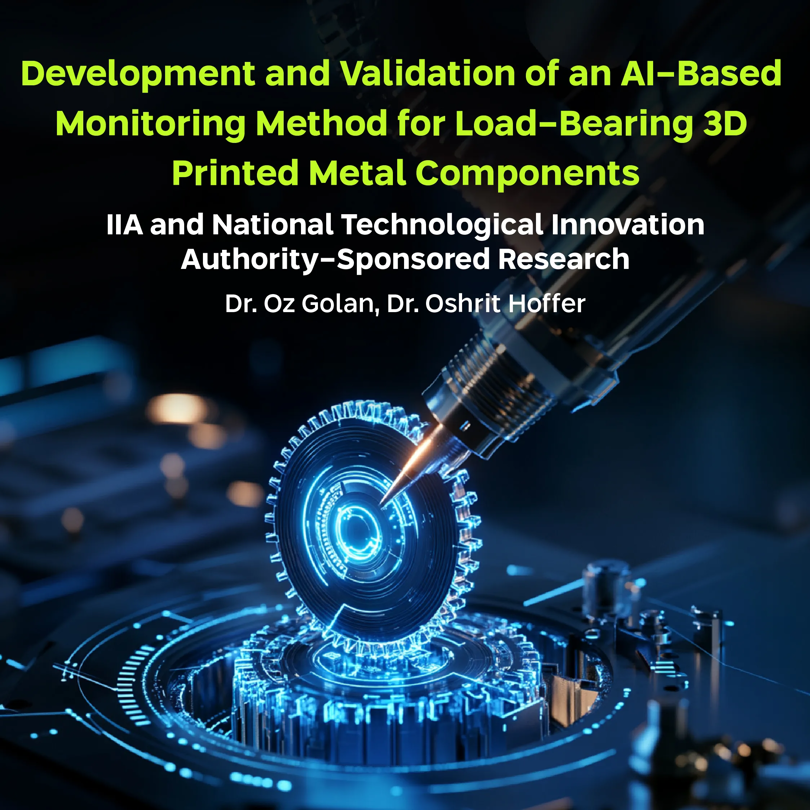
Development and Validation of an AI-Based Monitoring Method for Load-Bearing 3D Printed Metal Components
A groundbreaking research project combines ultrasonic resonance spectroscopy (PCRT) with artificial intelligence to develop an efficient, non-destructive testing method for 3D printed metal components. The study addresses a critical challenge in metal additive manufacturing: detecting structural defects that can compromise fatigue life and strength in load-bearing aerospace parts.
The innovative approach integrates CT scanning, PCRT data, and machine learning algorithms to create an automated pass/fail criterion for printed titanium, aluminum, and stainless steel components. This research aims to enable the safe implementation of 3D printed load-bearing parts in critical aerospace applications.
The project leverages six years of collaborative R&D experience between Afeka Academic College, the Metal Institute, and Israel Aerospace Industries, building on previous Innovation Authority consortium projects
Development and Validation of an AI-Based Monitoring Method for Load-Bearing 3D Printed Metal Components
Share a link using:
https://www.afeka.ac.il/en/industry-relations/research-authority/development-and-validation-of-an-ai-based-monitoring-method-for-load-bearing-3d-printed-metal-components/WhatsApp
Facebook
Twitter
Email
https://www.afeka.ac.il/en/industry-relations/research-authority/development-and-validation-of-an-ai-based-monitoring-method-for-load-bearing-3d-printed-metal-components/